The article It’s too big of a jump! showed that the scratches produced by a Shapton Pro 320 grit hone and a Shapton Glass 16k hone do not display a fifty-fold difference in depth or width, although the nominal grit size in those two hones differs by a factor of fifty. To further demonstrate this phenomenon, this article compares the swarf (the metal removed to form the scratches) from those two hones and the Shapton Glass 2k, which falls halfway between them in grit.

The first set of images show the swarf collected from a 320 grit Shapton after honing a carbon steel straight razor. In these images the bright objects are abraded steel, the majority of which have the familiar shape of turnings from machining waste, albeit at much smaller scale. The darker particles are broken or dislodged abrasive.
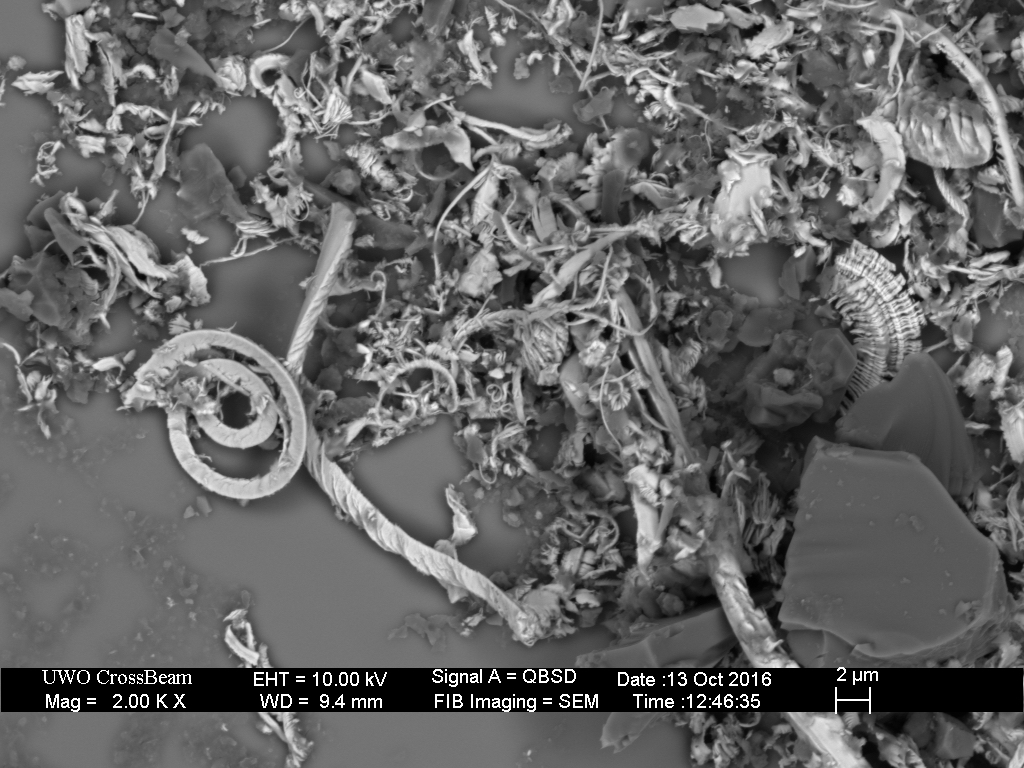


The swarf from the 2k Shapton glass stone ranges in size from approximately 2 microns to approximately 1/10 micron.



The swarf from the 16k Shapton glass stone ranges in size from approximately 1 micron down to less than 1/10 micron.




13 responses to “SWARF!”
And? What is the conclusion? Analysis?
LikeLike
This result is contrary to almost everything you will read elsewhere on the topic.
I prefer to let these observations stand on their own for the time being.
LikeLike
A couple variables you didn’t mention but which could add some context to the images: what was the baseline finish used before honing on these stones? We’re they all started from say a DMT 325 or 1k level honed baseline? If one started with a coarser finish it would seem that it would tend to produce larger swarf particles.
Next, what about pressure? I’m sure you were careful to keep it uniform, but it would be good to state that or otherwise let the readers/viewers know that you used more or less pressure for certain images.
I would also think it would be good to assure those reading that all tests were done on the same razor so as to avoid any alloy or hardness differences that might skew the results.
Otherwise, very interesting photos, good stuff! It always amazes me how much the swarf looks just like chips from machining even at this tiny scale!
LikeLike
I’ve had complaints about providing too many experimental details… I used one razor (vintage Lakeside Cutlery carbon steel) for all . The procedure was to lap the hone with an Atoma 400 diamond plate, rinse the hone thoroughly while rubbing with my gloved fingers. 100 back-and-forth strokes with the razor, rinse and rub to clean, another 100 strokes, rinse and rub to clean, finally a third set of 100 strokes and the slurry was collected with DI water and deposited on a silicon wafer piece for imaging. I used the same pressure I normally use for honing.
LikeLike
Wish I could edit posts for a few minutes! I also wanted to say that viewers should take note of the loose abrasive particles floating around in the swarf!
I can’t overstate how many times I’ve talked to guys who think that when they’re honing on “just plain water” that there’s no auto-slurrying going on. This happens on all but the most tightly bound hones and natural stones.
LikeLike
Hones do wear with use, we can see this when we lap them.
LikeLike
Informative and relevant.
LikeLike
Add a little color and these images look like beautiful little Jackson Pollock paintings. I suppose that is not really helpful. J
The removed metal “turnings” from a machine cutting tool look very similar, as you point out. The difference is that when machining, the metal falls away from the cut, whereas the razor edge is grinding into the broken abrasive and hard, removed metal pieces on a stone/hone slurry. This must do some damage to the edge. I wonder if placing the stone under running water for the final few strokes might refine the edge.
Comparing the slurry from these synthetic stones with the the “turnings” in slurry from a Japanese natural, Coticule or Escher might reveal something about the differences in the final edges. You have already shown that a Coticule edge does not need to be micro-convexed with a pasted denim strop. Why the difference?
Once the bevel is set, it seems like the magic, in making a razor keen enough for shaving, happens in the last few strokes on the hone, so the type of slurry, or no slurry, is important.
LikeLike
I don’t believe that the metal swarf damages the apex to any significant degree. The greater concern are the loose abrasive particles that fall into a position where they are higher than the surrounding grit particles and supported firmly enough to damage the apex on impact.
LikeLike
Every time I see a new post here my heart stops for a second. This must be the best blogg!
LikeLike
Dear Todd,
I have been following your post for a couple years, any policies if we would like to share some photos in your blogs?
Thanks for all the works.
Yung
LikeLike
feel free.
LikeLike
[…] the SWARF! article, I showed that size of metal chips increases with grit size, although more slowly than might […]
LikeLike